
THE STREAMLINER
The obsession in my life - Project "Kids Inheritance".
Like all forms of motorsport there are levels and hierarchy, and at the absolute top of land speed record setting is the "Streamliner".
This is the aerodynamic missile that sets the best speeds possible for an engine of a given size.
I love making small engines perform and so the 100cc class is my class, plus the fact that there are only 4 records for Bonneville that have stood unbroken since 1956, and one of these is for the 100cc class.
So how fast is fast!
The Bonneville record for S-BF, so that is streamliner blown fuel, is 138.000, set by H.Muller in August 1956 on an NSU.
The absolute world record is held by Buddfab, my heros, at 151 mph.
Not too shabby for an engine similar to most lawnmowers.
These are my targets for the near future.
Longer term, there is still one record held by Burt Munro, the legend of "The worlds fastest Indian", for 1000cc at 185.586mph set in 1967.
Whilst there is some superstition about this, i might have a go at beating it and getting into the exclusive 200 mph club for Bonneville. But we'll see...
The following article is about my journey to the salt with my own streamliner. Rumour has it, that there are only 12 or so motorcycle streamliners that are race fit in the world, i hope to join that exclusive club.
GOT TO START SOMEWHERE
Knew that draftman's board would be of use
The best way to start is to put something down on paper.
So i started a project book, and did a sketch of what i thought the bike should look like.
With time, it is actually a damn good sketch and the real thing is very close to the first drawing, however, this does belie, the huge amount of research and scale drawing comparison i did of both Buddfab (The record holders) and a Dutch team Aalt Toerson/Grune Tulp, who build a mobile bike but never made it so Bonneville.

HELP AT THE RIGHT TIME
Thank you - Chris Savidge
Whilst i would like to claim that i have done this project almost single handed, there have been key interventions from people that have been project savers, and Chris savidge was the first of these.
I had lots of sketches, good ideas and knew the direction of travel, but Chris took all of these and made them into proper CAD drawings, and even better then translated those into plywood templates that i could use to weld the first tubes int the configuration required to make a chassis.
I doubt i would have the skill to do this and it moved the project forward enormously, and very soon after i had a physical chassis.
Alas chris has been busy since those early days and not been able to continue the involvement, but i wouldn't want to diminish his contribution.

USING THE PLYWOOD TEMPLATES
Not as easy as i thought
Using the templates in theory should be easy, but of course the holes should be at the precise angle required to meet up with the next section.
So out came the bastard rasp and much filing tok place to make the angles and therefore the tubing meet up.
Then i could weld them together.
I should perhaps point out that i am building a prototype, and the real thing will be welded up by Paul Lumley, but as i have many mistakes to make on the way, and you cant grind back any welds on the real thing, i thought i would make my mistakes with a prototype. This theory is proving very sensible as i have had to alter many things.
The most obvious was i couldn't get in or out of the original design, what looked great on paper , wasn't in metal.

![]() | ![]() | ![]() |
---|---|---|
![]() |
MY WELDING HAS REALLY IMPROVED
taking shape nicely
At this point i must thank a long term friend, Stephen Malone, Co-Founder of Proseal heat sealing, who kindly donated a Kemppe mig welder to the project. This instantly improved my welding skills and is so easy to use and achieve good welds.
Some of the complex curve bending of the tubing round the roll cage area was done for me by a company near Leicester and they did a good job, as the tubing is 11/4" and 80 thou wall thickness or 34mm and 2.4mm in new money!
I really enjoyed this phase as it all comes together so quickly and you get a great sense of achievement.

STEAL WITH PRIDE
Great front end
One of the challenges i didnt really think through was how you move a 17ft long motorcycle around the country.
So luckily i found a 21ft long caravan chassis for sale on ebay just in Leicester and it absolutely suited my purpose. Si i welded on a central channel for loading ad unloading and bob became a close relative.
Now i could move the chassis to Lumley Engineering to have the front end welded in.
I had toyed with raked out telescopic forks but however i looked at it, there was a compromise in there, and i didnt want to have any on such an important part.
So Paul and i debated the front end used by Buddfab the current world record holders and how we could interpret it to suit my bike.
Now this isn't easy, as neither of us had ever seen it in the flesh , and it doesn't conform to anything you see.
The wheel more tilts than steers and the only fixing to the chassis is a 25mm track rod end, with 2 side tie bars, although the front end does have leading link suspension like most race sidecars, so some familiarity for Paul.
I cannot praise Paul enough for the great job he did.
![]() | ![]() | ![]() |
---|---|---|
![]() |
MOMENT OF TRUTH
Testing
Having fitted a metal plate as a seat, and a four point harness with arm restraints so that i could get used to steering with them on, it was the moment of truth to get it rolling and see if i could get it off the stabilisers i had welded on.
Now i was secretly scared that i would never be able to get the bike upright and off the stabilizers.
My friend Anders Jonsson had reverted to 3 wheels as he couldnt keep it upright on 2, both streamliners i had seen at Bonneville had failed to make the 1 mile flag, and most of us will have seen Guy Martin right off the Triumph streamliner from falling over too often, what hope did i have??
Well, back to that front end, as slow as 20 mph i was onto 2 wheels and stable, the bike just want to steer straight and stay upright, it must be the front end, its fantastic
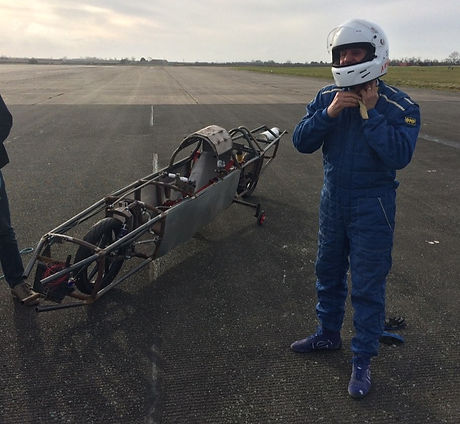
VIDEO FOOTAGE OF TESTING AT THE RUNWAY
Video Subtitle
It may appear very Heath Robinson, but being towed behind my Mercedes meant we knew how fast i was going, and Rob Comber could film the process and tell me what speed i was going, and when i was onto 2 wheels only.
We actually got up to 70 mph and every run i was onto 2 wheels and off the stabilizers by 20-25 mph.
I call that a result!!
NEED A BODY
Always was impatient
The usual way to construct a body is to make a male buck, take female moulds off it and then make numerous male copies.
But i only want one, although some of my friends think i will trash the body from falling over so often!
I wanted a quicker and hopefully easier way to do it.
So i constructed a skeleton using bamboo garden canes and wrapped it in chicken wire, to create a 3 dimensional framework.
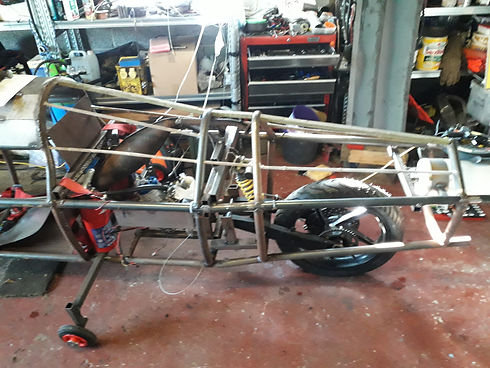
READ ALL ABOUT IT
The Roots
To actually make the skin of the body i had a cunning plan.
First i would cover the cane and wire frame with newspaper, you know like we did at school. Good old fashioned papier mache, and it worked pretty well.


ANOTHER SKILL LEARNT
But nearly just a sticky mess
When i was first supplied the fibreglass materials, it all went swimmingly well. the fibreglassing of the matting went to plan and the body shell looked pretty good.
However, and it was a big however, the first layer of gelcoat was a disaster as they didnt supply enough hardener, and the whole thing remained sticky after a week.
So i had to apply a second coat to skin over the first and create a sealed surface, even today some 3 months later there is a level of tackiness i dont think should be there, but i plan to paint it Donald Campbell Bluebird Blue.

BEING BRAVE AND ANGLE GRINDING THE FAIRING INTO SECTIONS.
Image Subtitle
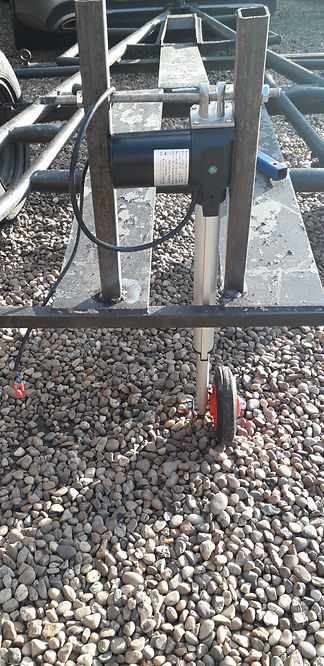
Testing the retractable stabilizer leg
The retractable leg is likely to be a linear actuator from a hospital bed, and i needed to know that whilst it is rated at 300kgs of lifting load, it could cope with 50mph sideways force, so i welded it to me trailer and took it for a spin down my local runway.
Needless to say it withstood the trial brilliantly, and the only issues now are the actual length and speed of retraction. Current speed is 5mm/s but you can get 50mm/s which is ideal
Change of colour and making progress
Its been a while since i added anything to the main pages and almost everything that has been going on is now on the blog section, but felt i needed to keep this section live as well.
Big date is the 18th of January, where UK lockdown permitting we are going to build the proper chassis, out of proper steel and using beautiful TiG welds, then we willbe on the final phase of the build as , every element then will be the real thing meant for Bonneville and NO botches!

So after many false dawns i took the plunge this November 2021 and have had the real chassis built. I took my Mig welded prototype to Lumley Engineering in Bridgwater, Somerset and they have converted it into a lovely Tig welded work of art and corrected many poor areas of Engineering such as the swing arm mount and the engine mounting system giving my flexibility to add a larger engine in the future and other options.
To keep the cost down i was the unpaid labourer, cutting tube to length, notching the tube and cleaning up the ends for welding. I certainly learnt many many new skills including using a milling machine.
